Oil Refractometer
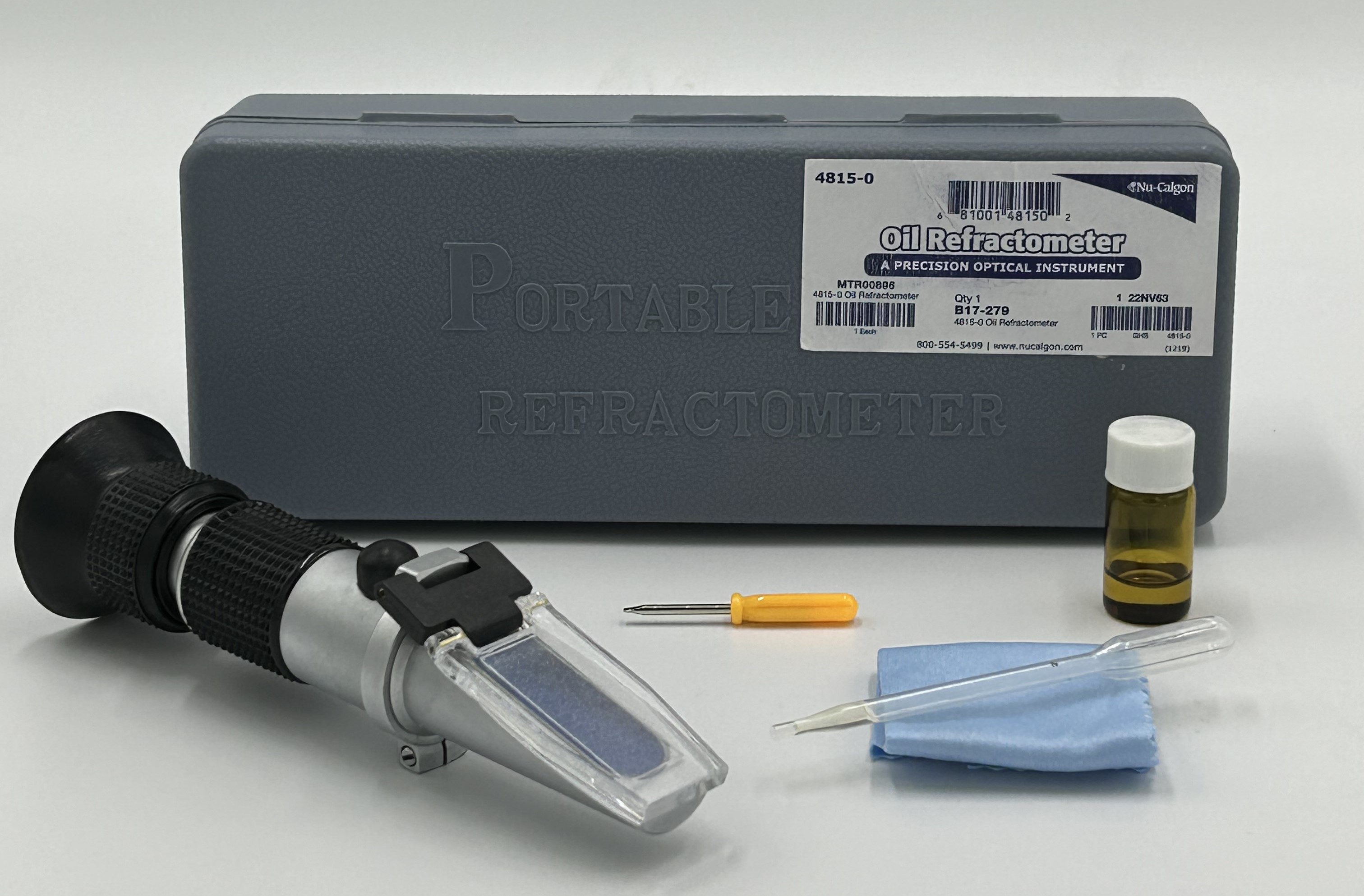
- An essential tool for retrofitting AC/R systems it simplifies the procedure and eliminates the guesswork
- Identifies lubricant residuals by measuring refractive index
- Can be calibrated in the field prior to each test
- Accurate and Efficient
Description:
This refractometer is a precision optical instrument that allows for the rapid and accurate determination of the refractive index of liquid solutions. It will specifically assist the service technician in determining the percent residual of oil remaining in a refrigeration system when converting it to a new refrigeration system when converting it to a new refrigeration oil. Such retrofits require converting the mineral oil to a polyolester (POE) or polyalkylene glycol (PAG), an alkylbenzene lubricant (Zerol®) to a POE, or a mineral oil to an alkylbenzene. With careful use and storage, this refractometer will provide years of service.
Packaging Size | Part Number | Additional Info |
---|---|---|
1 Each | 4815-0 |
Directions:
- Standardize with calibration fluid before first use and periodically thereafter. Keep both at the same temperature, or at 20ºC (68ºF).
- When testing an oil sample, place a few drops on prism face, and close and open the lens several times to “de-gas” the oil.
- Clean the lens and prism face after every use with a soft damp cloth.
- Plot numbers on chart on back page.
- Measure the refractive index of a sample of the new ICI Emkarate lubricant that you are going to use, as follows:
a) Place a few drops of the new (targeted) oil on the prism face.
b) Close and open the lens cover several times, and wait a few seconds to allow the solution to reach the refractometer’s temperature
c) Hold the refractometer up to a light source and adjust the focusing ring so that you can read the scale.
d) Note the scale position where the boundary line crosses the scale. This is the oil’s refractive index; plot this number as POINT 1 on LEFT SIDE Y axis of the chart. Also, make note of which ICI Emkarate lubricant that it is.
e) Clean the prism face and the lens cover using a soft, damp cloth, taking care not to scratch the lens cover. - Measure the refractive index of a sample of old oil being removed from the compressor BEFORE the start of the first oil change.
a) Test the sample following the above procedure.
b) Plot reading as POINT 2 on RIGHT SIDE Y axis. Again, mark what oil is being removed. - Connect points 1 and 2 with a straight line.
- Before each additional lubricant change, take a lubricant sample from the compressor and measure the refractive index.
a) Plot the reading point as POINT 3 on LEFT SIDE Y axis. - Draw a horizontal line (parallel to the X axis) from point 3 to where it intersects the line connecting Points 1 and 2. Mark this new point as POINT 4.
- From point 4, draw a vertical line (parallel to the Y axis) to the X axis, and mark this as Point 5. This is the percent residual of old oil in the compressor. Check with the compressor manufacturer or the producer of the new oil for the recommended maximum level of residual old oil in the system.
Note: The compressor should run 48 hours between lubricant changes to get a good mix of oils. False readings may be obtained when this is not done.
Product Information:
Literature Downloads
Download the product bulletin and other relevant literature here.
Labels
Download a low resolution file of the product label here.